Quality Inspector Job Description
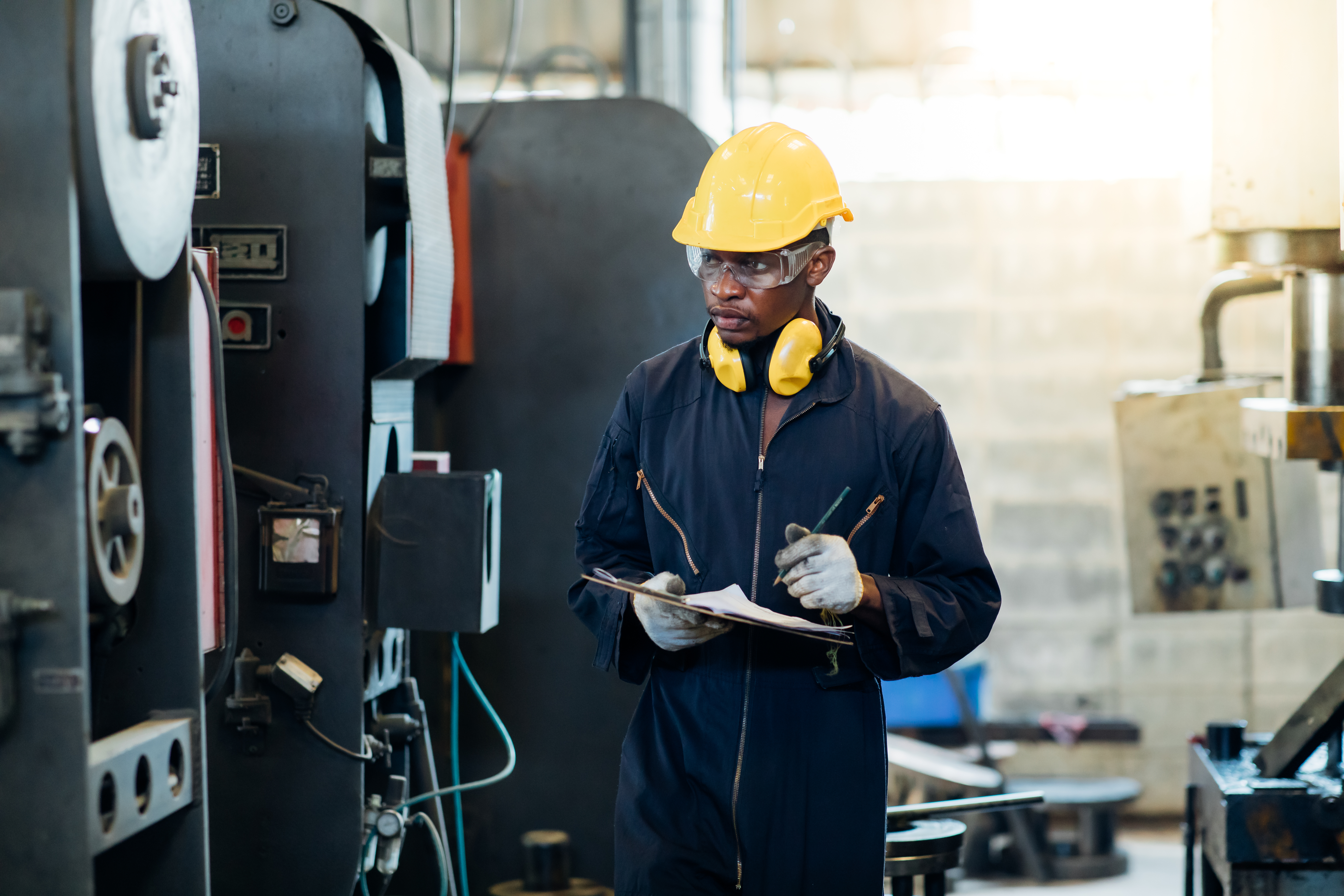
What Does a Quality Inspector Do?
A quality inspector is a professional who is responsible for examining products and materials to ensure they meet quality standards. They typically perform a variety of tasks including inspecting finished products, analyzing production processes, and documenting findings.
Quality Inspector Job Description Example
We are looking for a highly motivated and reliable Quality Inspector to join our team at our manufacturing facility in Pierre. Our Quality Inspector will be responsible for carrying out quality inspections on our products to ensure that they meet our high standards of excellence and that they are free from defects.
Duties and Responsibilities:
- Carry out quality inspections on our products
- Evaluate completed products for conformance to customer specifications
- Perform in-process inspections to ensure that processes are being followed correctly
- Keep accurate records of inspection results
- Investigate customer complaints and report any findings
- Participate in Root Cause Analysis to identify process improvements
- Ensure the facility is compliant with all safety and quality standards
Work Hours and Benefits:
This is a full-time position with standard hours, with the potential for overtime when needed. We offer competitive wages and benefits, including health, dental, and vision insurance.
Qualifications:
- High School Diploma or equivalent
- Previous quality inspection experience
- Attention to detail
- Excellent problem-solving skills
- Strong organizational and communication skills
- Ability to use inspection tools and equipment
Training and Education:
We will provide any necessary training to ensure our Quality Inspector is familiar with our processes and procedures. Additionally, we strongly encourage professional development and continuing education in the areas of quality assurance and quality control.
We invite qualified candidates to apply today and join our team! Please submit your resume and cover letter detailing your qualifications and professional experience. We look forward to hearing from you.
What to Include on a Quality Inspector Resume or Job Posting
Common quality inspector responsibilities
- Inspecting products for defects and conformance to quality standards.
- Documenting inspection results and maintaining accurate records.
- Performing tests and measurements to ensure product quality.
- Investigating customer complaints and identifying root causes of quality issues.
- Recommending corrective actions to improve product quality.
- Working with production staff to ensure quality standards are met.
- Training production staff on quality standards and procedures.
- Developing and implementing quality control systems.
- Analyzing data to identify trends and areas for improvement.
- Ensuring compliance with applicable regulations and standards.
Qualities & traits
- Attention to Detail: Quality inspectors must be able to identify even the smallest of defects in a product.
- Analytical Thinking: Quality inspectors must be able to analyze data and make decisions quickly and accurately.
- Communication Skills: Quality inspectors must be able to communicate effectively with colleagues and management.
- Technical Knowledge: Quality inspectors must have a good understanding of the product they are inspecting and the relevant industry standards.
- Problem-Solving Skills: Quality inspectors must be able to identify and resolve problems quickly and efficiently.
- Flexibility: Quality inspectors must be able to adapt to changing conditions and requirements.
- Patience: Quality inspectors must be able to work with precision and accuracy, even when the work is tedious.
- Interpersonal Skills: Quality inspectors must be able to work well with others in a team environment.
What a typical day looks like for a quality inspector
A quality inspector monitors the quality of products being manufactured or services being delivered in order to ensure that standards of excellence are being met. They inspect and test physical products, from raw materials to finished items, ensuring they meet quality criteria and industry standards. They observe and measure products to determine if they meet required specifications, use various testing equipment and collect data on product characteristics for comparison to required specifications. They document non-conformity issues, provide solutions, and report on inspection findings. They may also be responsible for auditing internal quality control processes. Quality inspectors may work in a variety of industries, including construction, manufacturing, and food service.
Compatible jobs and work history
Quality inspectors play an important role in ensuring that products meet customer standards and expectations. Although direct experience in the field is beneficial, individuals with a keen eye for detail and knowledge of relevant industry processes may still be suitable for the role. People from the following backgrounds may be able to transition into quality inspector jobs:
- Quality Assurance Manager
- Technical Inspector
- Process Engineer
- Quality Control Technician
- Production Inspector
- Quality Analyst
- Quality Coordinator
- Quality Auditor
- Reliability Engineer
- Supply Chain Manager
Similar Job Descriptions
We don’t have job descriptions for other roles in this industry yet. Check out all of our other job description templates for more.